A high-quality nonwoven product requires accurate, precision alignment of equipment. This can be a challenge in any manufacturing facility due to misalignment issues caused by equipment modifications and rebuilds, breakdowns, emergency repairs, regular maintenance, building settling, and corrosion.
Using Alignment Inspections to Optimize Equipment Efficiency
Misalignment of equipment can impact production performance, quality, and cost. It is important to have alignment inspections performed regularly as part of a preventive maintenance program.
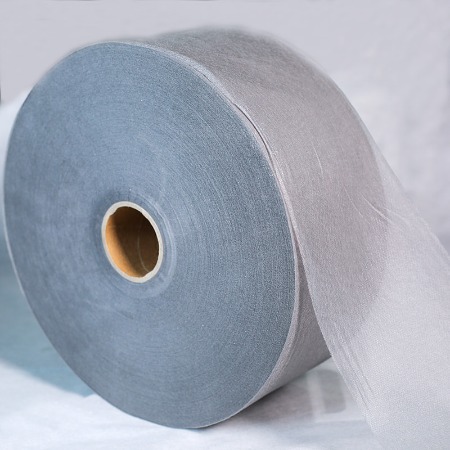
Inspecting equipment for misalignment can reveal a variety of common problems, such as baggy edges, soft rewinds, and poor fabric qualities. It is especially critical to inspect your nonwoven line at the start of a new installation, when your machine is still under construction, and after each significant change in your process or product specifications.
Alignment Problems In Nonwoven Processing
Spunbond and flash spun PP nonwoven fabric manufacturing is a highly complex process that requires precise alignment of equipment to standard tolerances. Having alignment inspections performed by an experienced company is crucial to minimizing costly equipment and product quality issues.
Using a Leica AT960 laser tracker, an OASIS Metrology Engineer precisely aligned each section of a line to ensure that all parts were running at the proper alignment tolerances. This helped eliminate problems with product waste, and allowed the line to run at a much higher capacity and produce a more consistent quality of end product.
Friction tests were performed on samples of % PP and PES spunbond nonwoven fabrics . The friction behavior of samples was evaluated using a horizontal working principle device, which consisted of anti-friction rollers, a sled , and a sled bed .