Advancements in nonwoven spunmelt machine technology can have several significant impacts on the performance and properties of the resulting fabrics:
Improved Quality: Advanced machinery often incorporates precision control systems, allowing for tighter control over various parameters such as fiber distribution, thickness, and uniformity. This results in fabrics with higher quality and more consistent properties, reducing defects and ensuring better performance in end-use applications.
Enhanced Strength and Durability: Technological advancements may enable the production of nonwoven fabrics with increased tensile strength, tear resistance, and overall durability. This improvement in mechanical properties can expand the range of applications for nonwoven materials, including those requiring higher levels of performance and longevity.
Innovative Fiber Blending: Modern spunmelt machines may offer greater flexibility in blending different types of fibers, including natural, synthetic, and specialty fibers. By combining fibers with complementary characteristics, such as strength, softness, or absorbency, manufacturers can create fabrics tailored to specific requirements and applications.
Customized Functionalities: Advanced technology allows for the integration of functional additives or treatments directly into the fabric during the production process. This capability enables the creation of nonwoven materials with enhanced functionalities such as antimicrobial properties, flame retardancy, moisture management, or barrier properties against liquids and particles.
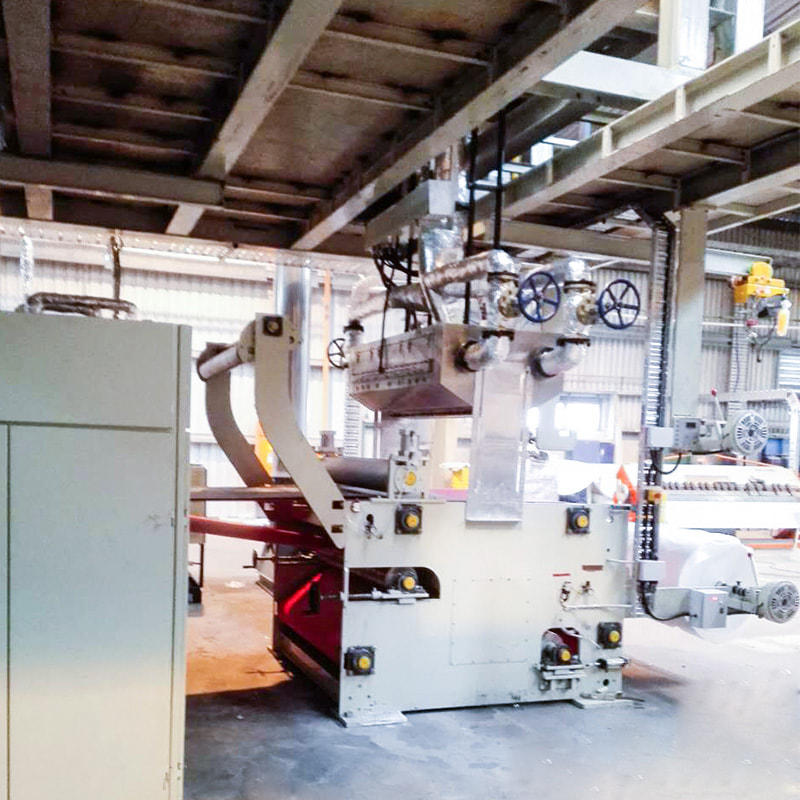
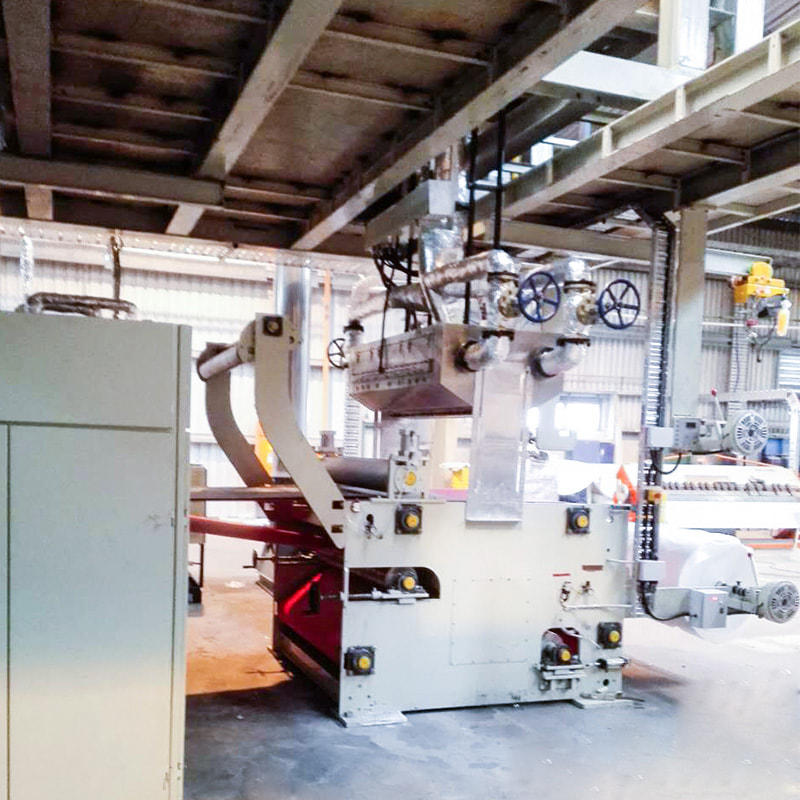
Microstructure Control: Advancements in meltblown technology, a key component of spunmelt processes, can lead to more precise control over fiber diameter and microstructure. This fine-tuning allows for the production of fabrics with specific pore sizes and filtration efficiencies, making them suitable for applications such as air and liquid filtration, medical textiles, and protective apparel.
Energy Efficiency and Sustainability: Modern nonwoven spunmelt machines may incorporate energy-efficient components and processes, reducing overall energy consumption and environmental impact. Additionally, advancements in material recycling and waste reduction techniques can contribute to a more sustainable manufacturing process.
Increased Production Speed and Efficiency: Advancements in machine design and automation can lead to higher production speeds and greater efficiency in material utilization. This not only enhances productivity but also reduces manufacturing costs and lead times, making nonwoven spunmelt fabrics more competitive in the market.