A double beam nonwoven production line is a complex and sophisticated piece of machinery used in the manufacturing of various nonwoven materials. To ensure consistent performance and minimize downtime, it is essential to implement effective maintenance and troubleshooting strategies.
Regular Inspection and Cleaning:
Conducting routine inspections of the production line components such as beams, rollers, belts, and conveyors is crucial. This helps in identifying any signs of wear, damage, or misalignment that can affect performance.
Regular cleaning of the equipment is also important to remove dust, debris, and accumulated residues. Clean equipment operates more efficiently and reduces the risk of malfunctions.
Lubrication:
Follow the manufacturer's recommendations for lubricating moving parts such as bearings, gears, and chains. Proper lubrication reduces friction, wear, and heat generation, extending the lifespan of critical components.
Use high-quality lubricants suitable for the operating conditions of the double beam nonwoven production line. Establish a regular lubrication schedule and ensure that all lubrication points are properly serviced.
Calibration:
Regular calibration of sensors, gauges, and control systems is necessary to maintain accuracy and consistency in production. Calibrate equipment according to manufacturer specifications and industry standards.
Verify and adjust settings such as tension control, temperature settings, and pressure levels to ensure optimal performance and product quality.
Monitoring Performance:
Implement monitoring tools and software to track key performance indicators (KPIs) such as production speed, material usage, energy consumption, and downtime.
Analyze performance data to identify trends, anomalies, or deviations from normal operating parameters. Use this information to make data-driven decisions and optimize production processes.
Training and Personnel:
Provide comprehensive training to operators and maintenance personnel on the operation, maintenance, and troubleshooting of the double beam nonwoven production line.
Foster a culture of proactive maintenance where employees are encouraged to report any abnormalities, perform routine checks, and follow standard operating procedures (SOPs) diligently.
Scheduled Maintenance:
Develop a detailed maintenance schedule that includes preventive maintenance tasks such as belt replacements, bearing inspections, alignment checks, and equipment servicing.
Keep accurate records of maintenance activities, repairs, part replacements, and equipment upgrades. Documenting maintenance history helps in identifying recurring issues and planning future maintenance tasks.
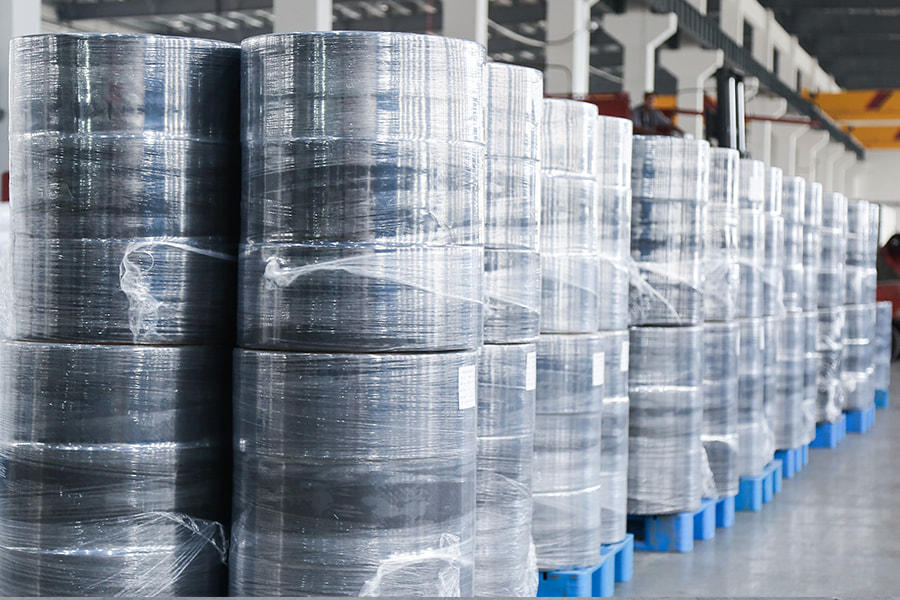
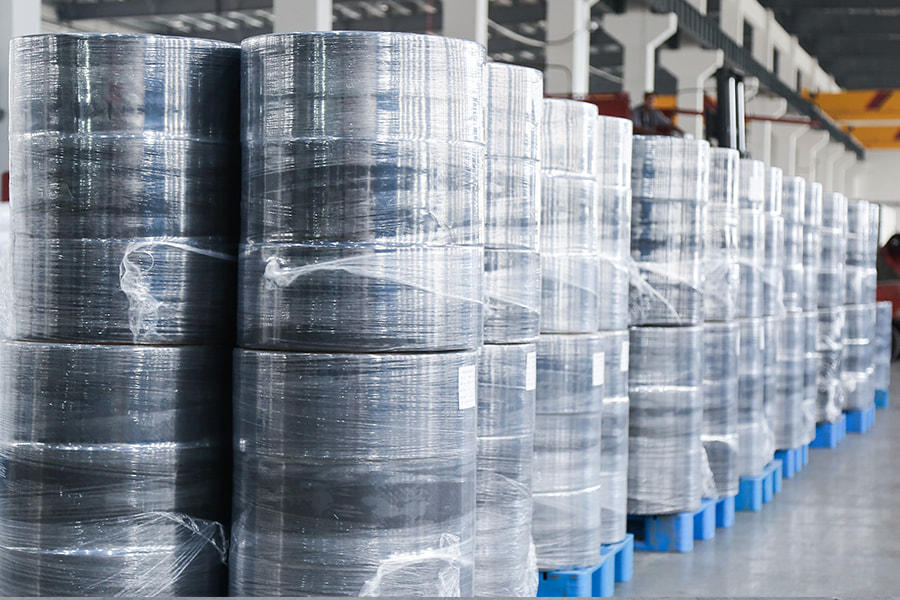
Troubleshooting Steps:
When facing production line issues, follow a systematic troubleshooting process:
a. Identify the problem by observing symptoms, alarms, or performance deviations.
b. Gather relevant information such as error codes, sensor readings, and production logs.
c. Isolate the root cause by inspecting components, connections, and settings related to the issue.
d. Implement corrective actions such as adjusting settings, replacing faulty parts, or recalibrating systems.
e. Test the system to verify that the issue has been resolved and monitor for any recurrence.
Collaboration with Suppliers:
Maintain open communication with equipment suppliers, service providers, and technical support teams. Seek guidance, spare parts, software updates, and best practices recommended by the manufacturer.
Stay informed about new technologies, upgrades, and improvements that can enhance the performance and reliability of the double beam nonwoven production line.