Products produced by a Nonwoven Fabric Machine using the thermal bonding process exhibit specific characteristics that make them suitable for various applications. The thermal bonding process involves applying heat and pressure to nonwoven fibers to create a cohesive fabric. Here are some key characteristics of products produced using the thermal bonding process:
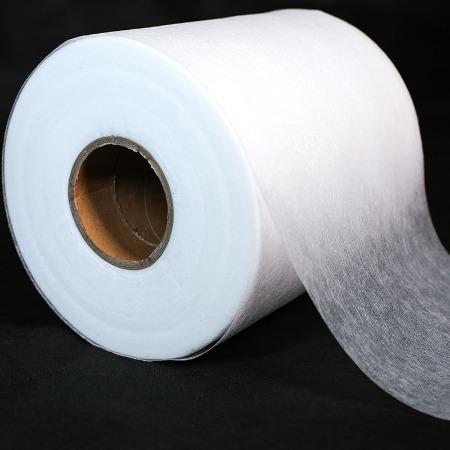
Strength and Durability: Thermal bonding imparts strength and durability to nonwoven fabrics. The application of heat and pressure causes the fibers to melt and fuse together, creating a cohesive and stable fabric structure. This results in a fabric that can withstand mechanical stress and wear.
Smooth Surface: Thermal bonding typically produces nonwoven fabrics with a smoother surface compared to other nonwoven production methods. This smoothness can be desirable for applications where a soft and comfortable touch is important, such as in medical textiles.
Consistency: The thermal bonding process allows for precise control over fabric properties, including weight, thickness, and density. This consistency is valuable in applications where uniformity is essential, such as in filtration media.
Breathability: Thermal bonding can be used to create nonwoven fabrics with varying degrees of breathability. By adjusting process parameters, it's possible to produce fabrics with specific air permeability characteristics, which can be advantageous in applications like hygiene products.
Softness: Depending on the choice of raw materials and process parameters, thermal-bonded nonwoven fabrics can be engineered to have a soft and comfortable feel. This softness makes them suitable for use in products that come into contact with the skin, such as diapers or wound dressings.
Resistance to Liquids: Thermal bonding can create fabrics with varying levels of liquid resistance. Some thermal-bonded nonwovens are designed to be hydrophobic (repel water), while others are hydrophilic (absorbent). The choice of treatment and additives can influence these properties.
Customization: The thermal bonding process is versatile, allowing for customization of nonwoven fabrics to meet specific performance requirements. Manufacturers of Nonwoven Fabric Machine can adjust process conditions, incorporate additives, or combine multiple layers to achieve desired characteristics.
Cost-Effective Production: The thermal bonding process is generally considered cost-effective due to its efficiency and the ability to produce fabrics with precise properties. This makes it a popular choice for a wide range of applications.
Hygiene and Sterility: Thermal-bonded nonwovens can be designed to meet hygiene and sterility requirements. They are often used in medical and healthcare products where cleanliness and infection control are crucial.
Environmental Considerations: Some thermal-bonded nonwoven fabrics are designed to be biodegradable or environmentally friendly, making them suitable for sustainable product applications.
Versatility: Thermal bonding is a versatile process that can be applied to a variety of fiber types, including synthetic and natural fibers. This versatility allows for the creation of nonwoven fabrics with diverse properties.