Finishing processes in a nonwoven fabric production line are the final steps that enhance the properties, appearance, and functionality of the nonwoven fabric. The specific steps for finishing can vary depending on the desired characteristics of the fabric and its intended use. Here are some common finishing steps that may be employed in nonwoven fabric production:
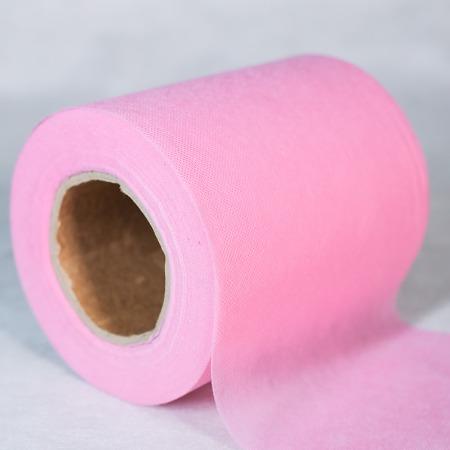
Calendering:
Calendering involves passing the nonwoven fabric through heated rollers under pressure. The combination of heat and pressure can compress the fabric, making it smoother, denser, and more uniform in thickness. The calendered fabric may have improved surface finish and opacity.
Applications: Calendering is often used to enhance the surface characteristics of nonwoven fabrics for printing, laminating, and some industrial applications.
Embossing:
Embossing involves passing the fabric through rollers with patterned surfaces. The pressure from the rollers embosses a design or texture onto the fabric. Embossing can be used for aesthetic purposes or to provide additional functionality, such as improved grip or appearance.
Applications: Embossed nonwovens are used in various applications, including decorative fabrics, wipes, and some hygiene products.
Coating or Laminating:
Coating or laminating involves applying a layer of material (e.g., adhesive, film, or another fabric) to one or both sides of the nonwoven fabric. This can impart specific properties, such as water resistance, barrier properties, or adhesion.
Applications: Coated or laminated nonwovens find use in applications like medical gowns, protective clothing, and filtration media.
Dyeing and Printing:
Dyeing involves immersing the nonwoven fabric in a dye solution to impart color, while printing applies patterns, designs, or logos to the fabric's surface. Both processes can be used to add visual appeal or brand identity.
Applications: Dyed and printed nonwovens are used in a variety of products, including disposable medical textiles, consumer goods, and decorative fabrics.
Antimicrobial or Antistatic Treatment:
Nonwoven fabrics can undergo treatments to add antimicrobial or antistatic properties. Antimicrobial treatments inhibit the growth of microorganisms, while antistatic treatments reduce static electricity.
Applications: These treatments are important in medical textiles, cleanroom apparel, and electronics packaging.
Flame Retardant Treatment:
Flame retardant treatments are applied to nonwoven fabric to reduce their flammability and enhance fire resistance. These treatments can meet specific fire safety standards.
Applications: Flame-retardant nonwovens are used in applications where fire safety is critical, such as upholstery, automotive interiors, and protective clothing.
Finishing for Softness or Hand Feel:
Additional processes may be employed to improve the softness or hand feel of nonwoven fabrics. Softeners or chemical finishes can be applied to achieve a desirable tactile quality.
Applications: Soft finishes are often desired in products like wipes, facial tissues, and garments.
Perforation or Slitting:
Nonwoven fabrics can be perforated or slit to create specific patterns or to facilitate tear-off sections. This can be important in applications where controlled tearing or access is necessary.
Applications: Perforated or slit nonwovens are used in items like disposable wipes, towels, and absorbent products.