The extrusion process in a Nonwoven Fabric Machine is a critical step in the production of nonwoven fabrics, particularly in processes like spunbond and meltblown. During extrusion, raw materials, usually thermoplastic polymers in the form of pellets or chips, are melted and then forced through specialized equipment called extruders to form continuous filaments or microfibers. Here's an overview of the extrusion process in a Nonwoven Fabric Machine:
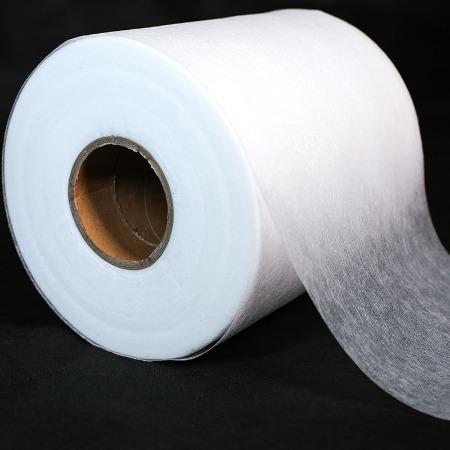
Raw Material Preparation:
The process begins with the selection of suitable raw materials, which are typically thermoplastic polymers such as polypropylene (PP), polyester (PET), or polyethylene (PE).
The raw material may be in the form of pellets, flakes, or chips. It is essential to ensure that the raw material is clean and free from contaminants.
Melting:
The raw material is fed into a hopper, which feeds it into the extruder.
Inside the extruder, the raw material is gradually heated, typically through electric heating elements or other heating methods. The temperature is carefully controlled to reach the polymer's melting point without overheating or degrading it.
As the material progresses through the extruder, it becomes a molten polymer.
Extrusion Through Spinnerets (Spunbond Process) or Nozzles (Meltblown Process):
Spunbond Process: In the spunbond process, the molten polymer is extruded through specialized spinnerets, which are essentially a set of fine, closely spaced holes or slits. Each spinneret hole corresponds to a filament in the final fabric.
Meltblown Process: In the meltblown process, the molten polymer is extruded through fine nozzles at high speed. The intense air pressure and hot air are used to attenuate the extruded polymer into micro-sized fibers. These fibers are much finer than those produced in the spunbond process.
Fiber Formation and Collection:
In the spunbond process, the extruded filaments are laid down onto a moving conveyor belt. The filaments form a random or controlled web as they cool and solidify.
In the meltblown process, the attenuated fibers are collected on a moving conveyor to form an ultrafine web. The high-speed air used during extrusion causes the fibers to stretch and become very fine.
Cooling and Solidification:
As the extruded filaments or fibers contact the conveyor belt or collection surface, they cool and solidify rapidly. This solidification process is essential for maintaining the shape and integrity of the fibers.