Quality control is crucial in the production of nonwoven fabrics using Spunmelt Machines to ensure consistent and reliable fabric quality. The integration of quality control measures may vary among different machines and manufacturers, but here are some common measures that are often implemented:
In-Line Monitoring Systems:
Basis Weight Monitoring: Sensors or scanners measure the basis weight of the fabric during production to ensure it meets the specified range.
Automatic Tension Control:
Tension Sensors: Automated tension control systems maintain consistent tension throughout the process, preventing variations in fabric thickness.
Temperature Control:
Heat Distribution Monitoring: Monitoring the temperature distribution across the machine to ensure uniform heating and melting of the polymer.
Airflow Control:
Air Permeability Monitoring: Systems to measure and control the airflow through the fabric, ensuring uniformity in permeability.
Fiber Distribution Control:
Fiber Laying Systems: Ensuring that the fibers are distributed evenly across the fabric to prevent irregularities.
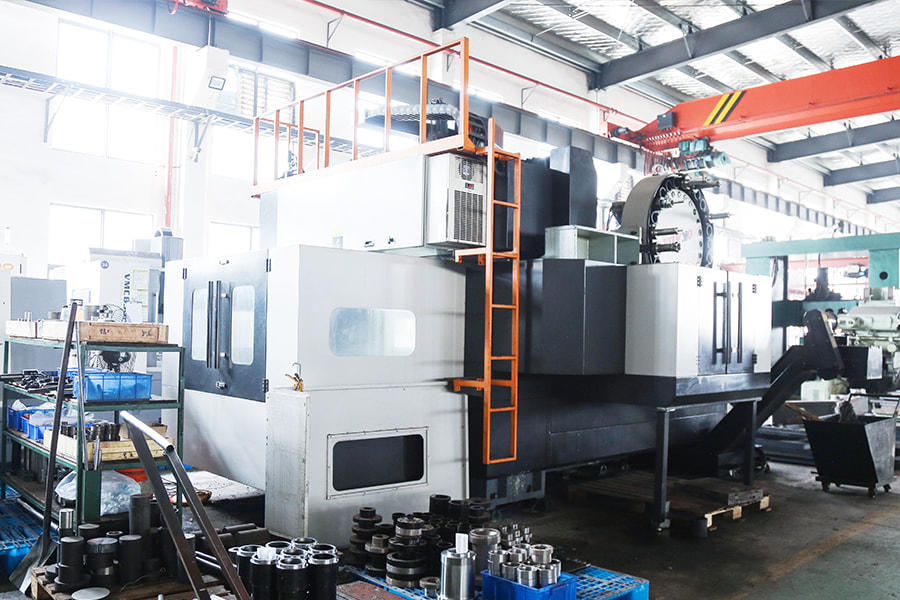
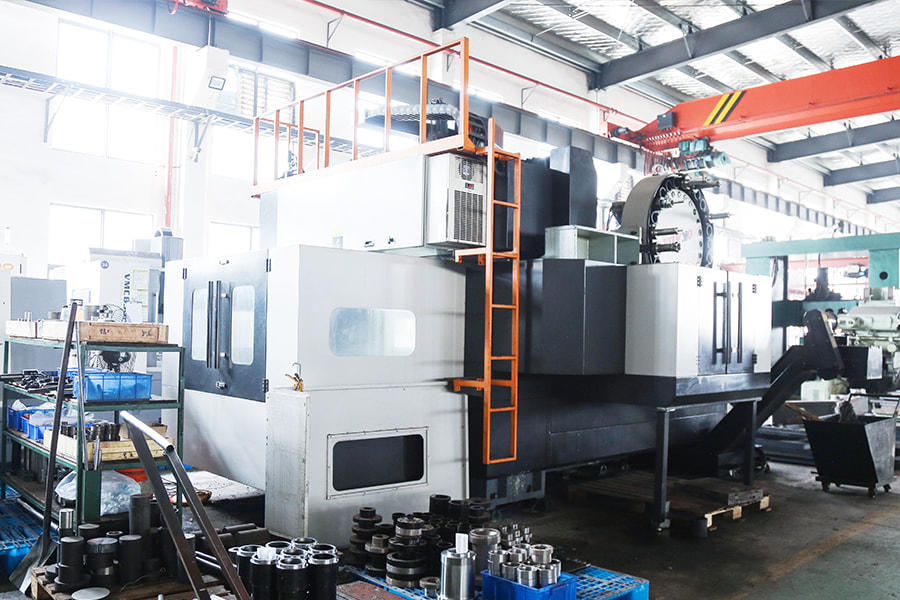
Web Formation Monitoring:
Web Formation Systems: Monitoring the formation of the nonwoven web to detect and correct any irregularities in the structure.
Electrostatic Charge Control:
Antistatic Devices: Implementing devices to control or eliminate electrostatic charges that could affect fabric quality.
Visual Inspection Systems:
Cameras and Vision Systems: Optical systems that inspect the fabric for visual defects, color variations, or other anomalies.
Thickness Measurement Devices:
Thickness Gauges: Instruments to measure the thickness of the fabric at various points, ensuring uniformity.
Moisture Content Control:
Moisture Sensors: Monitoring and controlling the moisture content in the material to maintain consistency.
Roll-to-Roll Inspection:
Inspection Stations: Implementing inspection stations at various stages to check the fabric quality as it moves through the production line.
Data Logging and Analysis:
Data Collection Systems: Collecting and analyzing data from various sensors to identify patterns or deviations and enable continuous improvement.
Alarm Systems:
Automated Alarms: Setting up alarms to notify operators in real-time if any quality parameter falls outside the acceptable range.
Sample Testing:
Random Sampling: Periodic sampling of produced fabrics for laboratory testing to validate quality against predefined standards.
Feedback Loop Systems:
Closed-Loop Control: Implementing closed-loop systems that automatically adjust Spunmelt Machines parameters based on real-time feedback from monitoring systems.